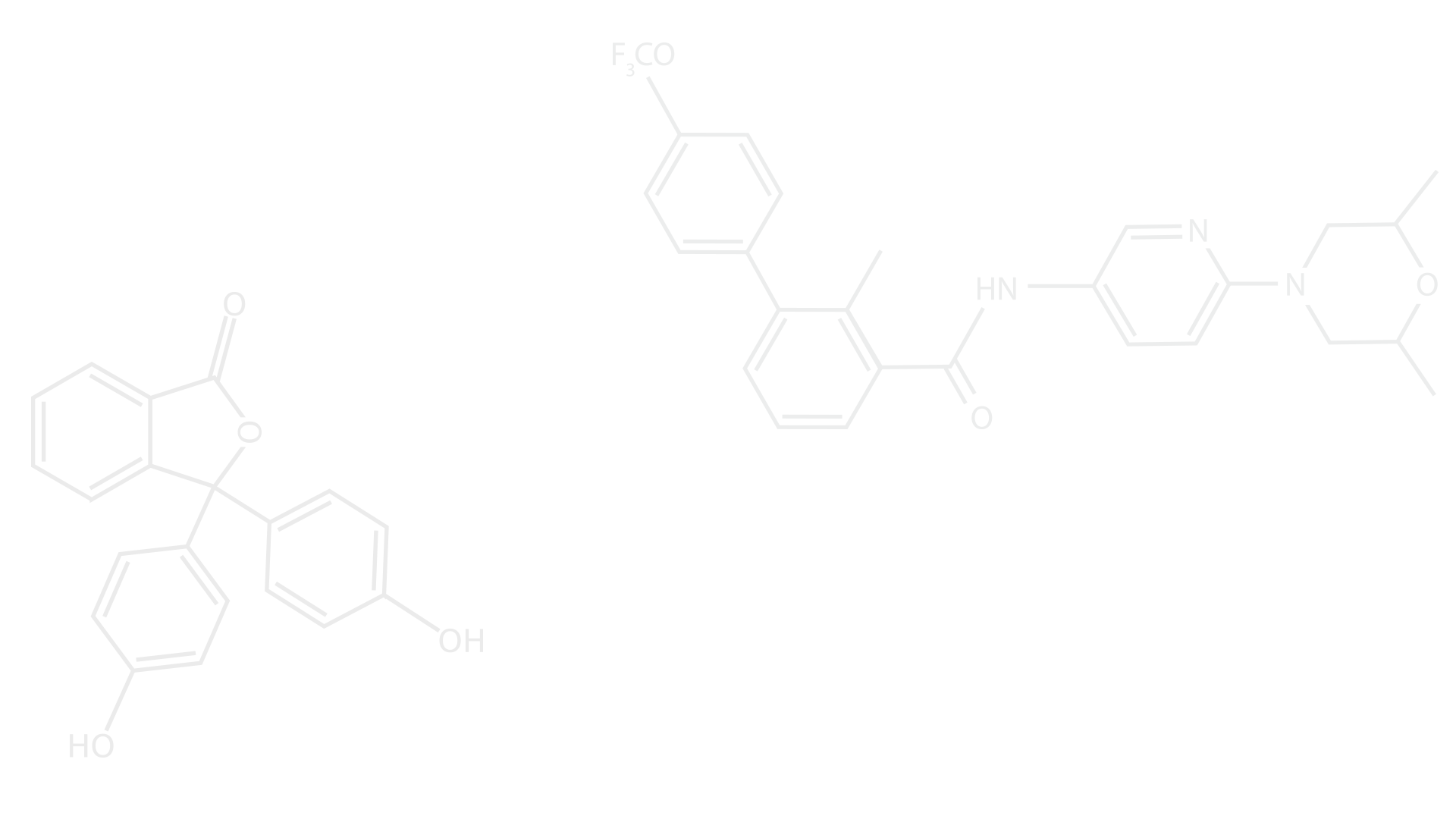
PUBLICATIONS
1.High‐Throughput Continuous Production of Shear‐Exfoliated 2D Layered Materials using Compressible Flows [Advanced Materials]
2D nanomaterials are finding numerous applications in next‐generation electronics, consumer goods, energy generation and storage, and healthcare. The rapid rise of utility and applications for 2D nanomaterials necessitates developing means for their mass production. This study details a new compressible flow exfoliation method for producing 2D nanomaterials using a multiphase flow of 2D layered materials suspended in a high‐pressure gas undergoing expansion. The expanded gas–solid mixture is sprayed in a suitable solvent, where a significant portion (up to 10% yield) of the initial hexagonal boron nitride material is found to be exfoliated with a mean thickness of 4.2 nm. The exfoliation is attributed to the high shear rates ( > 105 s−1) generated by supersonic flow of compressible gases inside narrow orifices and converging‐diverging channels. This method has significant advantages over current 2D material exfoliation methods, such as chemical intercalation and exfoliation, as well as liquid phase shear exfoliation, with the most obvious benefit being the fast, continuous nature of the process. Other advantages include environmentally friendly processing, reduced occurrence of defects, and the versatility to be applied to any 2D layered material using any gaseous medium. Scaling this process to industrial production has a strong possibility of reducing the cost of creating 2D nanomaterials.
2.Quantifying Defects in Graphene for High Performance Conductive Ink (Accepted at the MRS Fall Exhibit 2018)
Over the past decade, comprehensive investigations have been conducted to develop graphene based two-dimensional (2D) materials to harness their excellent and unprecedented properties such as high electrical conductivity, optical transparency, mechanical strength, and flexibility. To fully utilize these functionalities, a number of methods including chemical vapor deposition, liquid shear exfoliation, sonication, ball milling, electrochemical exfoliation and the recently conceived compressible flow exfoliation (CFE) have been successfully studied. However, these methods can introduce significant amount of defects during exfoliation into the graphene crystal structures that have a strong influence on their properties. This study is designed to compare the defect and flake quality between CFE and bath or probe sonication process for producing high-performance conductive ink from exfoliated graphene.
In our CFE process, graphite is rapidly jettisoned through a small orifice using high-pressure gases without the need for any time-based treatment, unlike other shear-based liquid processes. Shear-induced exfoliation occurs due to the high velocities that expanding and accelerating gases can achieve in small orifices coupled with viscous friction effects resulting in a high shear rate (γ>105 s-1) experienced by the graphite particles. In contrast, in the sonication methods, an ultrasonic transducer is used to induce unstable cavitation bubbles in a liquid medium, which upon their inevitable collapse emanate a shock wave. The energy of this shockwave is sufficient to fragment nearby bulk graphite powders into smaller lengths as well as thickness along the weak, secondary c-axis. But when the bulk particle is fragmented into smaller flakes, a good number of edge and basal plane defects are introduced into the flakes. The defect population increases as the time for sonication rises. The occurrence of a disorder-activated D peak at 1330 cm-1 in the Raman spectra of graphene is indicative of defects, in particular, those which disrupt the sp2 hybridization. Such defects can be interpreted to be the creation of new edges, vacancies or substitutions, with the ratio between the peaks intensities of the D to G peak (ID/IG) providing a qualitative indication of their population. In our study, we found the ratio of D peak to G peak is significantly less in CFE than that of bath sonicated graphene-ID/IG=0.66 for CFE graphene and ID/IG=1.1 for bath sonicated graphene. In contrast, the bulk graphite powder had ID/IG ratio of 0.62. The increased quantity of defects in bath sonication may be attributed to the prolonged sonication time which is well known to be responsible for reducing the flake length and hence, introducing more edges. The flake quality of exfoliated graphene was also verified using atomic force microscope (AFM) and transmission electron microscope (TEM).
